More than 30 years of Entrepreneurial Spirit and
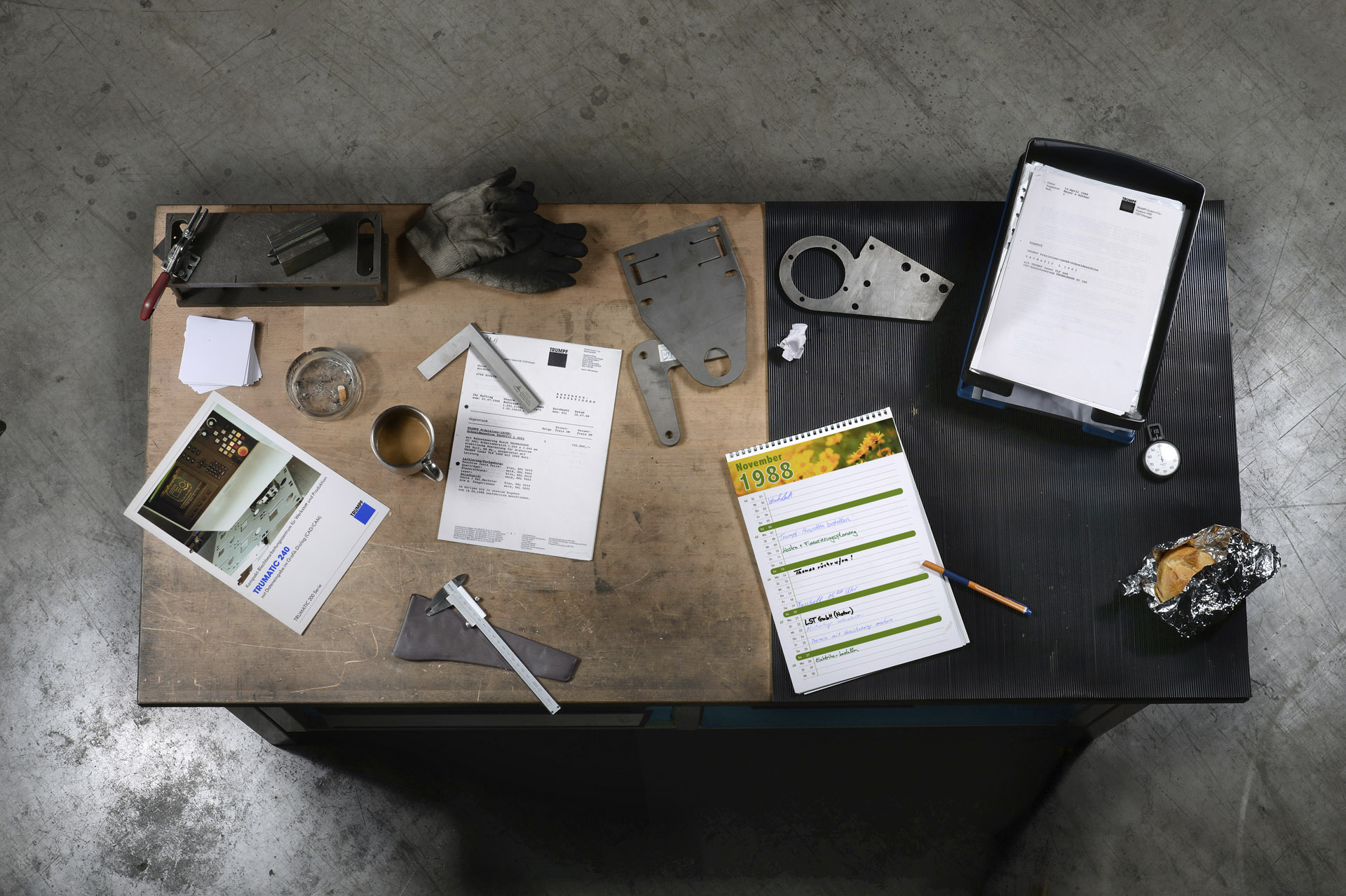
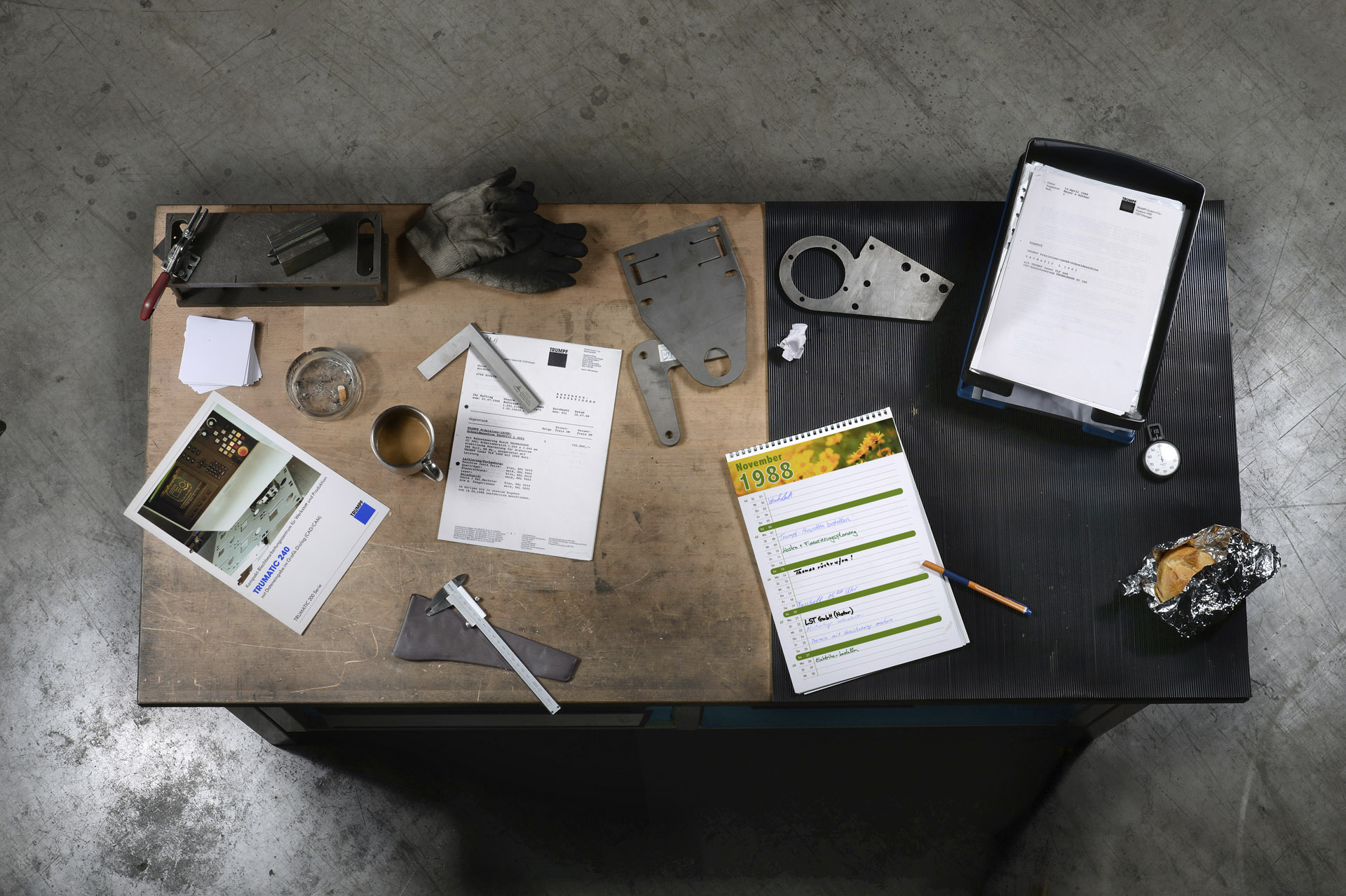
Our success story at a glance
Start of a success story
1988
On 22 November 1988, LST- Laserschneidtechnik GmbH is founded in the East Westphalian community of Hövelhof.
First orders
1989
With the TRUMPF Trumatic L 3003 for 2D laser processing, the young company LST starts production, set up in a rented production facility of just under 600 m². The first order is placed by ThyssenKrupp Umformtechnik.
New company building
1991
The spatial capacities of the rented production facility are now exhausted. The construction of our own company building with 1,500 m²of production area and directly adjacent office space with 250 m²is completed.
First 3D laser cutting machine
1992
LST imports its first 3D laser cutting machine from Australia, but just one year after purchasing, it is replaced by the TRUMPF Trumatic L 5000. The portfolio is also expanded with the Amada HFBO 1253 I press brake.
Now also 3D laser welding
1994
Thanks to some large orders, investments are being made in the third 3D system. The TRUMPF Lasercell 105 is equipped with the capabilities of 3D laser welding and 3D laser cutting of pipes. This is done with an additionally controlled rotary axis.
Series production arrives at LST
1995
LST is expanding its 3D laser production for special component processing with an additional Lasercell 105 system. This is used to manufacture stainless steel components for both development and series production.
First assembly
1997
By merging the areas of CNC folding technology, milling technology and the development of joining technology, the assembly production department is created. New technological standards are now also set by the welding robot acquired from Motoman.
First certification
1998
DIN ISO 9002 certification covers all business processes of a progressive company. To support production planning and control, the introduction of a PPS system begins.
Pendulum system
2002
The first pendulum system expands the machine park: The TRUMPF Lasercell 1005 enables 3D laser cutting technology with 2-station production. Pendulum systems shorten production times, which means that LST is increasingly accepting series orders.
Tested quality
2003
The company is certified according to DIN ISO 9001:2000. The minimum requirements for a quality management system for products and services, customer expectations and regulatory requirements are exceeded.
Expansion into the south
2004
In Schwäbisch Gemünd, in the industrial park Gügling-Nord, LST-Süd GmbH is founded as an independent company on 11 November 2004. The first ground is broken and LST now already employs 120 people.
Relocation and optimisation
2005
Eight months after the start of construction, start of production of the LST-Süd begins. The increased laser power and the first-class efficiency open up new perspectives for LST in optimising the price-performance ratio in production.
Successful course LST-Süd
2007
Already in the first two years, the order situation at LST-Süd in Schwäbisch Gmünd develops so positively that the production hall of just under 1,500 m² is no longer sufficient. The decision is made to double the production area to 3,000 m².
Start of production at Plant II
2009
LST acquires 21,000 m² of building land on Heinz-Sallads-Straße and starts construction of the elaborately structured Plant II. Plant II is to be ready for occupancy at the beginning of the year. In addition, LST is coping with the general economic crisis without making any redundancies.
Large-scale production
2010
LST makes use of technological developments: Four TruLaserCell 7020 with powerful 3 kW solid-state lasers are purchased. The shuttle system developed at LST marks the start of large-scale production in 3D laser cutting technology for the automotive industry.
Confirmation and enhancement
2011
The DIN EN 15085-2 CL1 certification certifies that LST meets the highest requirements for welding work in the application area of new construction of components for rail vehicles. In Plant II, the halls are enhanced by 1,000 m².
Enhancements will continue
2012
An HGV gate for loading and unloading the series components is planned and implemented to ease the logistics of the shipping area in Plant I. LST is awarded certification in accordance with DIN EN ISO 3834-2 for the highest standard in welding technology.
Laser marking technology sets new standards
2014
With the acquisition of a marking laser, LST is now able to label components in-house. Furthermore, the certification of an energy management system according to ISO 50001:2011 was introduced.
Quality management system confirmed
2015
The certification according to ISO/TS 16949 confirms the quality management system at LST. The fulfilment of customer-specific requirements in the automotive sector through uniform system and process considerations was confirmed.
Laser welding
2016
The integration of new laser welding cells increases capacity and improves processing speeds. Modern sensor technology and increased expertise set new quality standards.
Innovations, enhancements and automation
2018
Hall expansions at Plant II make it possible to significantly increase pipe laser processing. The first fully automated system developed by LST is put into operation. Automotive series made by LST. The modernisation of the 2D machine park meets the new energy efficiency requirements and increases capacities.